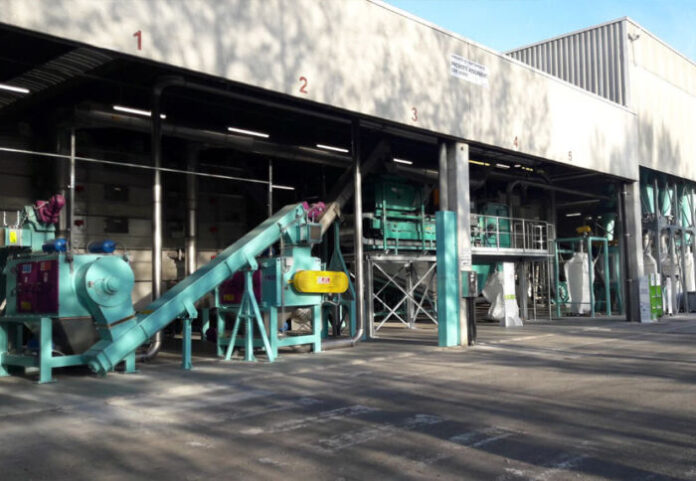
Sustainable development also means transforming used absorbent personal products, baby diapers, feminine pads and products for incontinence into resources for the environment and for the economy. The technological recycling process was developed by an Italian company, Fater Smart, part of the Fater Spa group, that produces brands of absorbent products.
The plant is located in Treviso and is capable of recycling used absorbent products, obtaining precious secondary raw materials. No longer landfills or incinerators, but recycling to separately obtain plastic, cellulose and super absorbent polymer. New life in new applications in line with the principles of Circular Economy and with a “carbon negative” balance.
How does the recycling process work? The collection of dirty diapers is the fundamental prerequisite of the recycling system. The collection is carried out by specialized operators through the door to door, at centralized facilities such as hospitals, nursing homes, nurseries or in municipal collection centers. The collected material arrives at the diaper recycling plant, where the recovery process begins: after the accumulation of waste in the access door, it is stored and transported to the machine’s central units.
In the second phase the organic component is eliminated. Inside the autoclave, thanks to the combination of pressure steam, the absorbent products used are sterilized and the constituent materials are pre-separated. Afterwards, ribbons transport the products into the dryer, inside which they are perfectly dried. This process allows the elimination of bad odors and the elimination of all potential pathogens.
In the final phase, a series of separator batteries in series, through a system of rotating cylinders, allows the separation and recovery of secondary raw materials. From each tonne of this waste, 150 kg of cellulose, 75 kg of plastic and 75 kg of super absorbent polymer are obtained.
Cellulose has multiple applications ranging from use in paper mills to the production of fabrics such as viscose. The super absorbent polymer can be used in the horticultural industry, in the insulation of electric cables and in other industrial applications. Finally, the recovered plastic allows new productions of objects for multiple areas, from home to school, from offices to companies. In keeping with the principles of the circular economy, every waste returns to a new life, with new productive uses.
The environmental and economic advantages are evident: first of all the elimination of absorbent products from landfills and incinerators which avoids emissions equivalent to those absorbed by over 30 thousand trees each year. If extended to the whole national territory, this industrial system would allow to reduce the climate-changing emissions produced every year by over 100 thousand cars.
Fater Smart however does not stop and aims to extend its technology by creating new plants, of small dimensions, in more areas to avoid long transports, costly and impacting from an environmental point of view. Zero kilometer systems, therefore, that can be realized thanks to the collaboration with operators in the world of waste that operate locally. The company from Treviso, in fact, has adopted a business model that provides for the development and sale of diaper recycling machines, which will allow their technology to be exported to Italy and the world.